By Nicole Jacques, Rhumbline Communications
Every autumn, boats in colder climates get covered in white long before the first snowfall. Shrink-wrap season colors in an ominous landscape across our boatyards: oceans of plastic on boats today are threatening to become our real oceans’ undoing tomorrow. It’s a bad look for us. Still, our customers request shrink wrap every year, and we’re in the business of providing customer service.
Appearances aside, most of us would welcome an alternative that works for both our customers and us. But shrink wrap waste seems like a necessary evil, which may be why our industry’s first efforts to go greener have been through recycling it instead of eliminating it. A handful of grassroots resource-recovery efforts around the country have grown into major operations that are responsibly removing hundreds of thousands of pounds of shrink wrap from landfills annually. If your boatyard hasn’t had the opportunity to become part of one of these programs, you’re definitely missing out. These processes have become so streamlined that it’s often easier to pay for their services than to pay for an extra dumpster every spring.
In fact, cost doesn’t have to be a barrier at all to going greener with shrink-wrap recycling. Admittedly, extra labor is unavoidable because all doors, zippers, and ties have to be separated from the plastic. However, participation in a state- or organization-sponsored recycling program tends to be inexpensive at roughly $12 to $14 per boat. Boatyards can generally pass off these relatively small costs to the consumers on the front end of the process by building them into the initial shrink-wrap invoice.
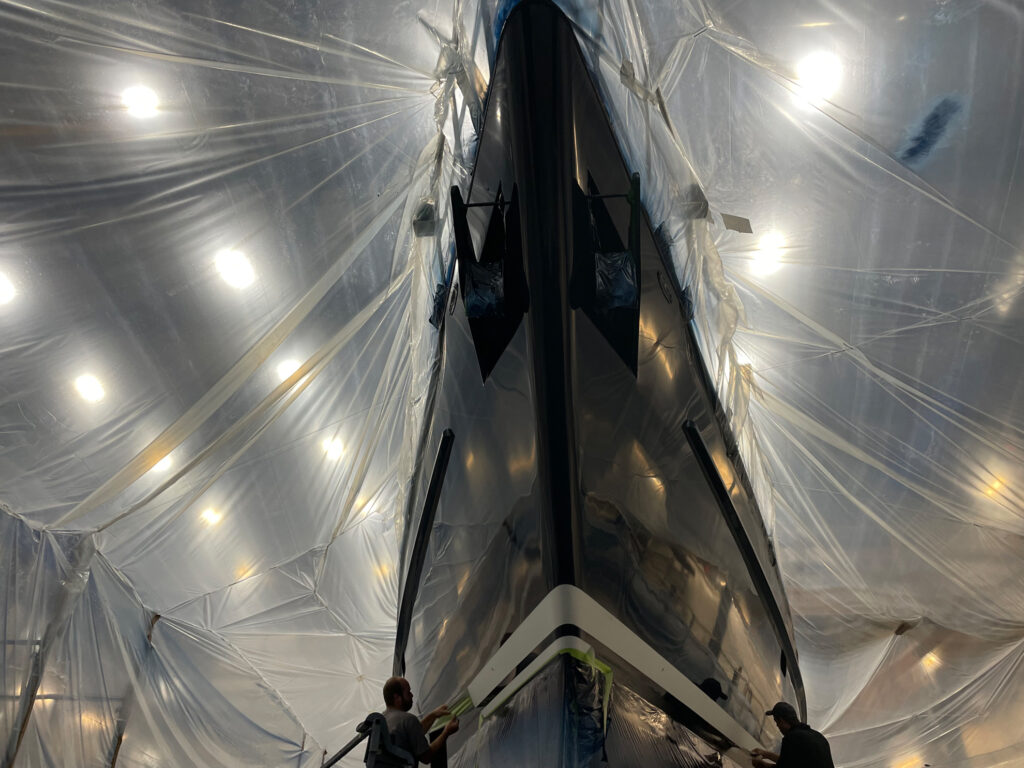
[firstlight.jpg] Plastic used to tent boats for paint or sandblasting is not recyclable.
Most of the costs charged by recycling facilitators go toward moving the shrink wrap from yard to processor to recycler. According to Victor Horton of the Maine Resource Recovery Association, the 44,000 pounds of shrink wrap amassed annually for recycling in Maine moves through one of two processors in the state that collect it, bale it, and load it onto trucks. Rhode Island Marine Trades Association’s Jen Huber says their system offers an alternative to centralized collection facilities to make it easier for yards to participate. RIMTA members’ 190,000 pounds of shrink wrap are picked up directly from the boatyards by PF Trading of Massachusetts and then processed off site. From there, trucks in both states — among others — get filled to the brim with bales of plastic wrap and then head to the recycling “marketplace.”
This used shrink wrap lands at one of several outlets around the country, which pay roughly fifteen cents per pound for it. Then the real recycling happens. Or does it? One of the most popular of these facilities is New Jersey-based TerraCycle, which promises to turn boatyards’ discarded plastic into raw materials that can be used in new manufacturing processes. After years of accepting delivery of hundreds of thousands of pounds of shrink wrap and other plastics shipped from around the country, TerraCycle revealed in 2021 that its warehouse had filled up with products that weren’t at all recyclable. Much of the plastic they’d collected had particles of dirt, chemicals, or contaminants that prevented it from being processed. That left TerraCycle literally holding the bag with tons of waste. Several lawsuits later, TerraCycle had to settle out of court over allegations of unlawful and deceptive recycling claims.
Alternative recycling outlets are sparse but do exist, including a Virginia-based plant that’s currently accepting a lot of the shrink wrap from the East Coast. This NexTrex® facility processes shrink wrap into “lumber” for Trex Decking, the composite deck boards, railings, and outdoor furniture used for residential houses. Sold at major retailers like Home Depot and Lowe’s, Trex claims its products are made of 95% recycled materials, so the company relies heavily on relationships with commercial entities in industries laden with plastic waste — like the marine industry. But no one seems to have calculated the carbon footprint of hundreds of trucks full of plastic waste driving hundreds of miles to these processing facilities.
Clearly, the existing recycling practices are far from perfect. And the truth remains that a landfill continues to be a less expensive, easier option. A Rhode Island-based company called Bioaqualife is hoping to change the product we use instead of the process. Founder Simon Milne launched a biodegradable shrink wrap alternative into the marketplace just over a year ago. Easily identifiable by its pale green patina, Bioaqualife wrap is currently available in the marine and construction markets for boat winterization, tenting, and vapor barriers. The “biowrap” purports to be fully decomposed within three to five years of its end-of-life interment into a landfill.
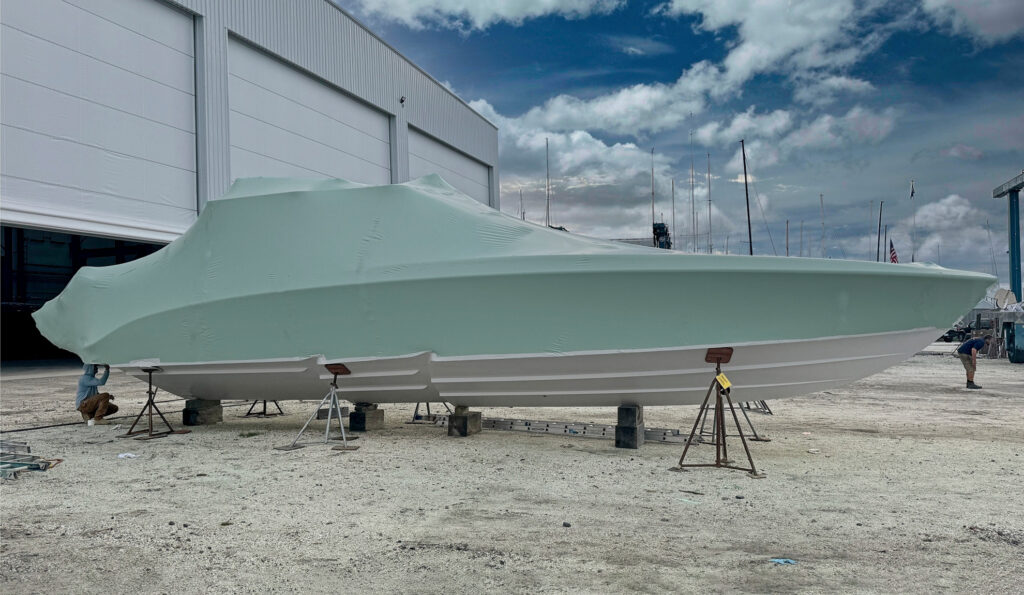
[bioacqualife.jpg] Bioaqualife boat wrap is recognizable by its pale green color.
That’s right: used Bioaqualife is intended to go to the nearest dump instead of hundreds of miles away to a recycling processor. It’s installed on boats the same way traditional wrap is, so it can replace products without disrupting any existing practices at a boatyard. It’s tear- and puncture-resistant, pliable, and purportedly requires less heat for the installation. And, no, it won’t break down while it’s on boats, even over long periods of time outdoors in the sun and elements. Bioaqualife’s proprietary ingredient requires landfill conditions to attract microorganisms that ultimately consume the wrap, leaving nothing behind — not even microplastics. The wrap essentially turns into microbe meals.
Milne is still cooking up new recipes for success in the marine market. “If we really look at what we do, we can make even more products biodegradable,” he says. Think vacuum bags in boatbuilding. “That’s one of our goals in the future.”
Bioaqualife is currently distributed by Kellogg Marine Supply at a cost that’s about 10-12% higher than other shrink wrap. This extra expense is comparable to the recycling costs of regular shrink wrap, at approximately $14 for the average boat. All of the products are biodegradable in the landfill — including wrap used in painting or sandblasting that’s too contaminated to be recycled. Could this mean we’ll have guilt-free trips to the dump?
I asked a friend who works in waste-management policy development for her thoughts. She was hesitant to offer an opinion since the product is so new and still in the early stages of scientific testing. Perhaps, she suggested, there are some even newer technologies on the horizon? With high hopes, she sent out an information-seeking email to ten environmental professionals from state, university, and nonprofit organizations that are on the cutting edge of sustainability innovation. She asked them to share with me any success stories, new ideas, or emerging tech addressing the problem of shrink wrap. The email generated a palpable silence. Eventually one researcher replied diplomatically that, “it’s still a tough go, to get shrink-wrap material back into some useable form,” before extoling the “great opportunity for leadership” available to whatever innovative entity or person may come up with the answer we were all quietly waiting for.
That silence gets louder as yet another shrink-wrap season begins. Journalists, politicians, and industry leaders are talking resoundingly about microplastics, climate change, and ocean warming. Busy boatyard managers are understandably spending more time attending to the health of their businesses than to the health of our industry or our oceans, but we can’t stick our fingers in our ears and ignore it. The bravest among us listen intently and become early adopters of new technologies — and we owe them our thanks. For the rest of us, let’s keep open ears and open minds.
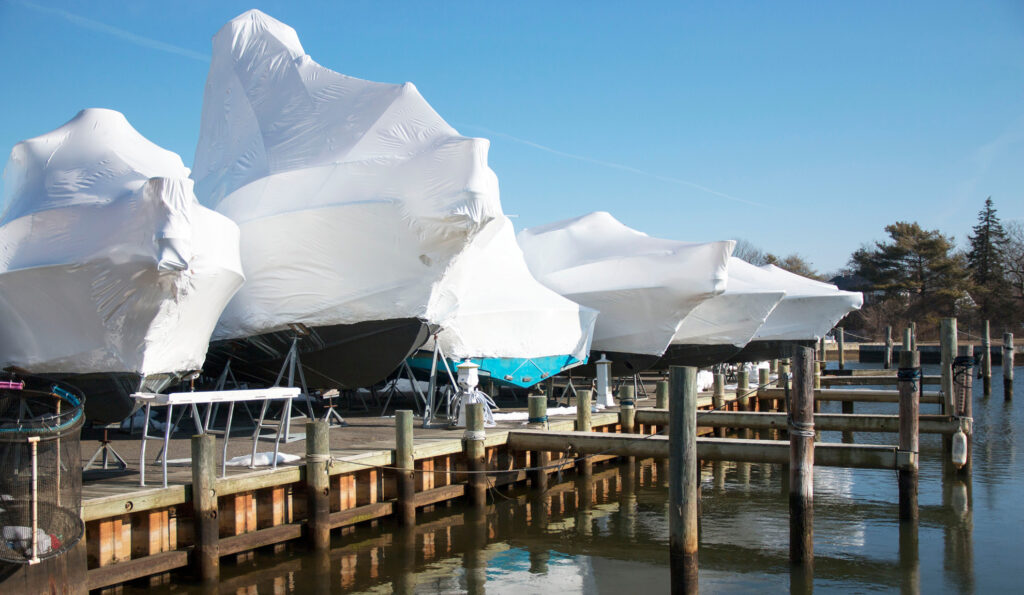
[genericshrinkwrap.jpeg] Shrink-wrap season starts in September in colder climates.